Circular Approach to Bearing Reuse
Separate collaborations, involving Sverull and Nomo, to recycle and reuse worn steel bearings, not only saves costs but also conserves valuable resources and reduces the carbon footprint for major Swedish manufacturers.
The core of both initiatives is remanufacturing of used bearings to its original specifications using reused, repaired, and new parts instead of making a new product. This creates an innovative loop that saves time, money, and raw material. The remanufacturing of bearings is gaining popularity among large industrial customers and is advancing sustainability in traditional industries.
Cutting emissions and costs at Swedish paper mills
One of Sverull’s customers is a world leading company in high-performing paper and packaging materials whose plant in the Swedish city of Norrköping, is one of Europe’s largest paper mills. The bearings on its paper rollers are critical to the production of premium-quality kraft printing paper.
As part of their strategy to cut CO2 emissions and become climate neutral, the customer got together with Sverull to discuss how to reduce the supply chain carbon footprint.
“They were looking at everything that could help them achieve climate neutrality, and one part was to try to reduce their consumption of bearings,” says Per Helgesson, Key Account Manager at Sverull. “We created a systematic loop for them that would enable their bearings to be remanufactured, meaning they would be refurbished rather than be sent for scrap. This saves a lot of CO2 but it also has financial benefits, as a remanufactured bearing costs only 70 percent of buying a new one.”
That saving is multiplied because the bearings on which the paper rollers rely can be reprocessed four to five times, vastly extending their lifetime.
Early damage detection by preventive maintenance
The collaboration involves preventive maintenance technicians inspecting bearings for wear, removing bearings for remanufacturing, and sending them to Swedish bearing manufacturer SKF for reprocessing. Sverull then replaces the removed components with remanufactured bearings it keeps in stock.
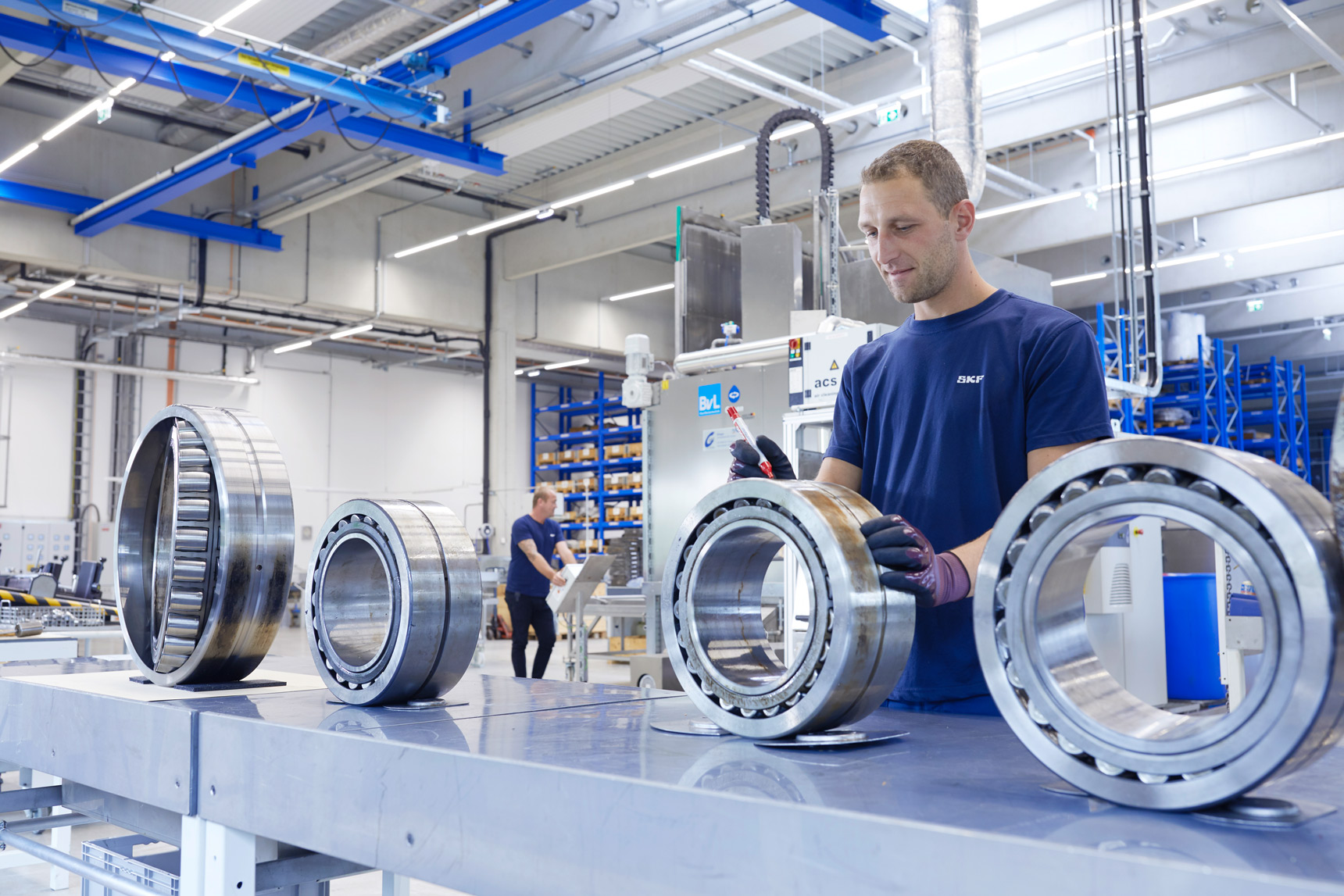
Photo: SKF
The customer bearings are produced to order. In the past, this meant waiting for six to ten months for new ones. Using remanufactured bearings directly from Sverull’s inventory significantly shortens lead times. The warranty for a remanufactured bearing is the same as for a new, and the expected lifetime is identical.
Sverull’s Managing Director, Fredrik Stjernholm, says the loop enables the customer to secure its supply chain. “During the pandemic our service meant that the customer had no problems supplying bearings for their machines, even when supply chains virtually collapsed. If a bearing fails, they know they can be up and running very quickly with a remanufactured component.”
Reducing the carbon footprint
The environmental benefits are also substantial. As well as contributing to sustainability by maximising the bearing’s lifetime, each remanufactured bearing helps reduce carbon emissions.
Per says: “Last year, one customer plant saved 2.9 tonnes of CO2 through bearing remanufacturing. That’s equivalent to a car journey more than halfway around the globe.”
Fredrik says the project is a perfect example of how Sverull can help customers optimise their processes and improve their value chains.
“Our whole strategy is to be a partner for safe, reliable, and sustainable operation,” he says. “It really lines up with our desire to create customer value through sustainability and cost efficiency.”
Pioneering a strategic alliance
More than 20 years ago, Nomo started a collaboration with Swedish steelmaker SSAB to cut costs within the steel production by refurbishing worn-out bearings instead of throwing them away. This initiative led to a collaboration involving Nomo, SSAB, and Timken, a global leader in bearing manufacturing.
At SSAB, Nomo assumes an important role in overseeing the remanufacturing possibilities of worn industrial bearings employed in the rolling of high strength strip steel, some of which weigh up to 80 tonnes. Subsequently, these bearings are dispatched from Nomo’s service centre to Timken’s facility in Romania for the recycling process.
Exemplary expertise in a demanding task
The evaluation of bearings demands a high level of proficiency gained over years of experience. Typically, the bearings are analysed in Nomo’s facility servicing the housings that accommodate the bearings. These housings are consistently refurbished after pre-defined service intervals and rarely need replacement.
Sales representative at Nomo, Johan Östholm, has gained extensive expertise in bearings, specifically those used within the steel industry. Johan is tasked with evaluating SSAB’s bearings, approaching their service life, and identifying candidates for remanufacturing.
Photo: SSAB
”Mastering the visual analysis of bearings and estimating their ability for remanufacturing demands considerable time,” Johan asserts. ”It’s based on mutual trust between the customer, Nomo, and Timken.”
He underscores the critical importance of timely action, and the need to prevent bearings from surpassing their optimal remanufacturing threshold. ”The material wears out gradually, and we cannot afford the risk of bearing failure, potentially incurring millions of euros
in downtime.”
Significant efficiencies
The bearings used represent some of the largest and most expensive in the industry and refurbishing them amounts to approximately half the cost of procuring new ones. The cost savings are substantial as well as savings in CO2 emissions.
”Our collaboration has meant significant savings for SSAB, over the past decade and a half,” Johan explains. ”Previously discarded bearings are now contributing to a sustainable and profitable business model benefiting both sides.”
When a bearing need replacing, Nomo promptly supplies identical remanufactured bearings from the inventory. This quick replacement approach helps SSAB save money by avoiding the long delivery times for new bearings. Johan has witnessed an increase in interest among manufacturers to refurbish bearings instead of throwing them away, driving a surge in remanufacturing demand. This upswing has led to extended lead times. Still, it is notably quicker, more cost-effective, and sustainable alternative compared to buying a new one,” Johan concludes.
Leading company in industrial services, mechanical maintenance, and product sales with expertise in electromechanics, bearings, transmissions, seals, and pumps.
Founded in 1970
Part of Axel Johnson International since 2007
Headquarters in Jönköping, Sweden
Number of Employees 105
Market Presence Sweden
A leading multi-brand specialist for mechanical transmission products and related services for the Nordic industry.
Founded in 1948
Part of Axel Johnson International since 2000
Headquarters in Täby, Sweden
Number of Employees 176
Market Presence Sweden, Finland, Norway, Denmark, China